Chemical Processing of Phosphate
The phosphate mineral as it exists in the ground is not soluble and is hard for the plant to access. To provide the plant with the phosphate it needs, in a form it can take up through its roots, the phosphate rock is converted to phosphoric acid. It is that acid that is used to make fertilizer.
Most of the phosphoric acid produced, about 90%, is used to make agricultural products. Another 5% is used to make animal feed supplements. The remaining 5% percent is used in a wide variety of products including soap, toothpaste, and soft drinks. There is phosphate in camera film and inside light bulbs. It helps make steel harder and water softer. It plays a part in dyeing cloth and in washing clothes. Phosphate is used in the cement a dentist uses on teeth and in the fluids used to drill for oil and gas. It is part of making cloth and helps to polish aluminum. And, phosphate is also used in making plastics, shaving cream, and bone china dishes.
Phosphoric acid is produced at a fertilizer manufacturing facility (sometimes called a chemical processing plant) that is not connected to the mining operations. In central Florida’s mining district, fertilizer manufacturing plants are located between Plant City and Bartow. Though the mining is moving south to Hardee, DeSoto and Manatee counties, the processing plants will not move. It less costly to ship the rock back to existing plants for processing than to move the processing operations and the phosphogypsum stacks associated with the process.
After the phosphate is separated from the sand and clay at the beneficiation plant it goes to the processing plant.
There it is reacted with sulfuric acid to create the phosphoric acid needed to make fertilizer. The principal fertilizer product of the industry is diammonium phosphate (DAP), made by reacting ammonia with the phosphoric acid. DAP fertilizer is water-soluble and will be available for the plants to take up through their roots.
The sulfuric acid that is needed to convert the phosphate rock into phosphoric acid is also produced at the chemical processing plant using liquid (molten) sulfur, most of which is shipped to a Florida port and trucked to the processing plants. Since the energy crisis in the 1970s, most Florida phosphate companies capture the heat released in the burning of sulfur and production of sulfuric acid and use it to produce steam. The steam is used to produce the heat required to concentrate the phosphoric acid and also to produce electricity to run the plant. Typically, plants produce most of the energy they need and some sell a portion to the area commercial energy provider.
When sulfuric acid is reacted with phosphate rock to produce phosphoric acid, a by-product calcium sulfate (gypsum) is also produced. This by-product gypsum is called phosphogypsum. There are approximately five tons of phosphogypsum produced for every ton of phosphoric acid product produced. Phosphogypsum, like natural gypsum, is calcium sulfate, but it contains a small amount of radioactivity due to the radium that naturally occurs in Florida phosphate rock. Because of this trace amount of radioactivity, a 1992 U.S. Environmental Protection Agency (EPA) rule bans most uses of phosphogypsum. Since it cannot be used, the majority of all the 30 million tons produced annually in Florida is stockpiled in stacks.
Phosphate Chemical Processing Plant Flowsheet
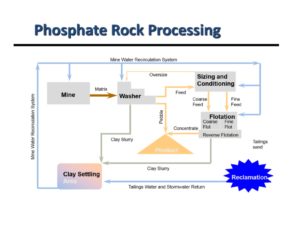
Click here to open a larger image of the flowsheet.